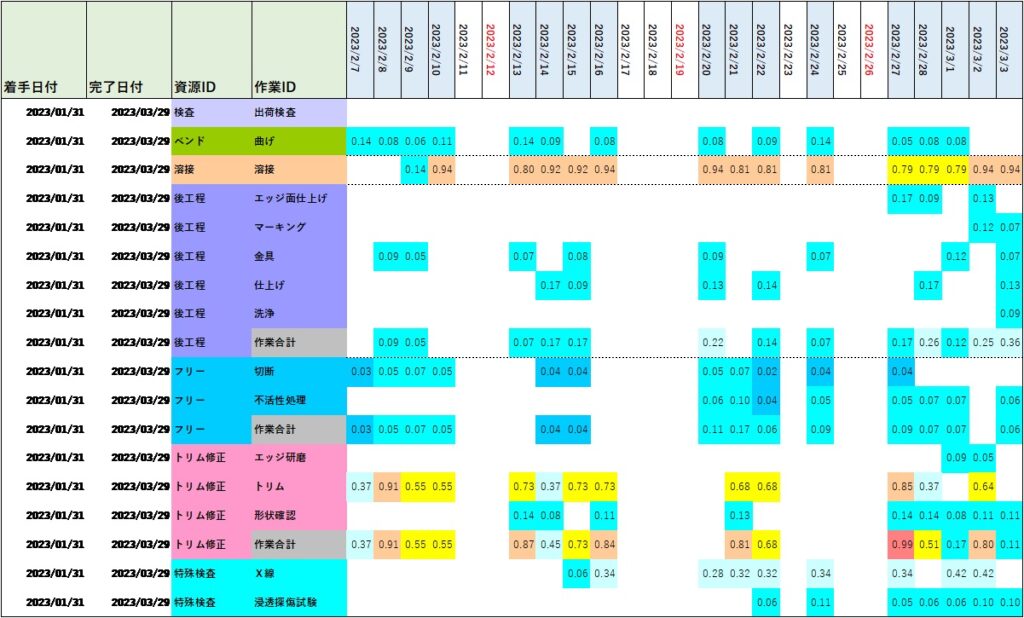
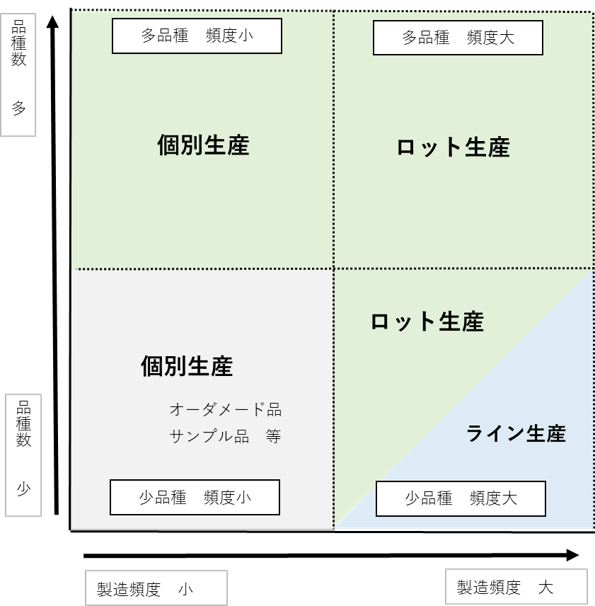
生産計画の最適化とTOC
製造業は発注者の「必要な時に、必要なだけ」という要請に応じる必要があります。その為、生産プロセスに様々な工夫をして対応しています。
対策は、中間在庫保持、装置、人、置き場、治工具等、多岐に渡ります。
多要素の管理は難易度の高い操作です。その為、熟練の生産計画担当に依存するケースも多々あります。
それは計画立案をKKD(経験と勘と度胸)に頼っていることになります。結果、そのノウハウの継承に苦労します。また、その計画妥当性を第三者が検証する手段が有りません。
イスラエル出身の物理学者エリヤフ・ゴールドラットは、小説建てにした「ザ・ゴール」の中で、TOC(制約理論)という考えを提唱しています。これは生産計画立案の聖域にメスを入れ、シンプルな考え方で見える化を進める手段でした。
TOC(制約理論)とは
日本TOC協会のサイトにTOCを次の様に紹介しています。「どんなシステムであれ、常にごく少数の要素または因子によって全体のパフォーマンスが制限されている」。これは数珠繋ぎの生産プロセスがボトルネック工程に制約されているという伝言です。
またTOCをゴールドラットは「フォーカス」だと一言で述べています。そしてフォーカスするとは、「何をすべきかを決めると同時に、むしろ何をすべきでないか決めること」と見立てています。 つまり、全体に均一に対策を取ることではない。一番大事だと思われることに注力すべきという事を語っています。
制約と非制約
入力と出力が連携していく工程は、多足動物ムカデが前進していくことに似ています。ムカデが前進していく時の速さは意外と早いそうです。それは節ごとにある足をリズムよく運動させているからです。
ライン生産方式はそのムカデ行動です。つまり、各工程時間が均等になる様にラインを設計・運用します。その事で特定の工程がボトルネックにならない工夫をしています。また、万が一ある工程で障害が発生した場合は、トヨタで言う「あんどん」を引きます。全体の工程を停止し、問題解決を図ってから再開始することで作業の偏りを防ぎます。
少量多品種の生産は、個別生産が主となります。その為、初めから調和のとれた生産ラインを設けることができません。必ずボトルネック工程が存在し、全体の必要期間やスループットを左右します。そのボトルネック工程が全体の生産フローを決定するキーとなります。他の工程はボトルネック工程に従属して、非制約な振る舞いになります。
TOCはシンプルな問題解決方法
TOCとは、ボトルネックに着目する問題解決方法といえます。そして通常組織は少数の制約しかうまく扱えません。
日本TOC協会の2016年の公開資料「The Most important TOC insitghts」の文言です。「組織はごく少数の制約しかうまく扱えない-普通はただ一つ」。ある工程のリードタイムを決定すべき変数が多数の場合に当てはめます。これは、最適化時変数が相互作用し生産フローは不安定になることを示しています。「はじめの一歩」は制約であるボトルネック工程に着目することがだと主張しています。
これはある意味シンプルな解決策です。実は、KKD(経験と勘と度胸)計画担当者が各工程で独自のKPIを定め決定します。KPI要素を事前定義しますが、TOCはそのことに近い方法論と言えます。
ボトルネック工程には、ゆとり(バッファ)が必要
TOCを取り入れる場合、考慮ポイントの一つとして、バッファ(ゆとり)があります。
ある計画を行う時に使用する各因数の値は通常平均値です。例えば、その因子が人に依存するケースと。ベテランと新人が平行して作業する場合の所要量計算は通常平均を使います。しかし当然現場作業では揺らぎが生じています。
ベテランの数値で計画した時は、アクシデント時に計画が守れないリスクを持ちます。非制約工程はアクシデント時リソースに余裕が有り、遅れを吸収することができます。しかしボトルネック工程ではそうは行かないのです。その為、ボトルネック工程に対して、ある程度のゲタをはかせておくことが、結果的に全体の工期を守る計画立案することにつながります。
NAPX計画の利用について
NAPX計画ではある工程に対して、ひとつの仮想的な資源IDを設定します。これはその工程の生産性を左右する因子(人、装置など)から、決定的なファクターを資源IDと定義して、所要時間やバッファ時間を定めるルールです。そのことで、ゴールドラットの主張するフォーカスをするための方法を提供しています。是非ご自身の生産現場で試用して是非を判断してください。